Wir können unsere Klimaschutzziele in Deutschland erreichen, wenn der Bau von PV-Anlagen deutlich gesteigert wird. In Zukunft sind für die Stromversorgung um die 20 Quadratmeter Photovoltaik je Einwohner erforderlich. Die dafür notwendigen Flächen am Gebäudebestand sind mit rund 12.000 Quadratkilometern auf den Dächern und 6.000 Quadratkilometern an den Fassaden grundsätzlich vorhanden [1]. Die Flächen bieten ein technisches Potenzial von 1,6 Terawatt Solarleistung. Um möglichst viele Gebäudeeigentümer von der Photovoltaik zu überzeugen, sollte die Integration der Module in Dach und Fassade nicht nur ökonomisch und funktional erfolgen, sondern auch ästhetische Aspekte berücksichtigen.
Zudem erfüllen diese Anlagen zusätzliche bauliche Funktionen. Als bauwerksintegriert werden solche PV-Anlagen (BIPV) bezeichnet, die neben der solaren Stromerzeugung weitere Gebäudefunktionen übernehmen, zum Beispiel die der Dacheindeckung, der Fassadenbekleidung oder des Sonnenschutzes. Die Solarbranche bietet dafür Indachsysteme und PV-Fassadenmodule sowie photovoltaische Sonnenschutzelemente an.
Der Anteil von BIPV in Deutschland ist jedoch noch verschwindend gering. Das Schweizer Forschungsteam SUPSI ermittelte für 2023 eine installierte BIPV-Anlagenleistung von 312 Megawatt in Europa und 37 Megawatt in Deutschland [2]. Mit den Zahlen für den Gesamtmarkt verglichen, ergibt sich hierzulande ein BIPV-Anteil von lediglich 0,25 Prozent. Andere Länder sind weiter: So erreichte Frankreich einen BIPV-Anteil von 2,7 Prozent, die Schweiz sogar von fast sechs Prozent.
Warum es BIPV in Deutschland schwer hat ...
Hoher Genehmigungsaufwand und hohe Kosten: Für BIPV gelten in Deutschland zusätzliche bautechnische Anforderungen, insbesondere die Musterbauordnung MBO (Brandschutz) und die Musterverwaltungsvorschrift Technische Baubestimmungen MVV TB (unter anderem Glasbau) (siehe auch GEB 09-2022, Fachregeln und Prüfmethoden für PV-Fassadenmodule). Die in der Photovoltaik international üblichen Einordnungen und Prüfungen in Brandschutzklassen sowie die mechanischen Prüfungen nach den Normen IEC 61215 und IEC 61730 reichen nicht aus. Außerdem müssen die technischen Baubestimmungen des Deutschen Instituts für Bautechnik (DIBt) auf geltende Glasbau- und Fassadennormen sowie bei PV-Indachanlagen die Regeln des Dachdeckerhandwerks beachtet werden. Hinzu kommt, dass internationale Prüfungen oder Zulassungen meist nicht anerkannt werden.
Alles in allem erfordert das zusätzliche brandtechnische, konstruktive und mechanische Prüfungen bei zertifizierten Prüf-
organisationen. Der Zulassungsprozess ist zudem aufwendig und langwierig. Kein Wunder, dass in Deutschland nur acht PV-Anbieter die allgemeine bauaufsichtliche Zulassung (abZ) beziehungsweise die Bauartgenehmigung (aBG) für ihre Produkte erhalten.
Besitzen PV-Module für eine Fassade keine DIBt-Zulassung, muss eine Genehmigung im Einzelfall bei der örtliche Baubehörde vorgenommen werden. Das kostet zusätzliche Zeit und verteuert das Bauen. Die erhöhten Kosten haben zum Teil auch damit zu tun, dass Sondermaße oder ein spezielles Modullayout (Glasart, spezielle Verkapselungsfolien, verstärkte Rahmenkonstruktion) benötigt werden. Am Ende kosten BIPV-Produkte bis zu 300 Prozent mehr als Standardmodule.
Die Kostenproblematik gilt es allerdings differenziert zu betrachten. Denn inzwischen sind Standard-PV-Massenmodule günstiger als die meisten Baustoffe. So sind PV-Module mit Quadratmeterpreisen von derzeit um die 30 Euro konkurrenzfähig zu günstigen Dacheindeckungen wie Trapezblech oder Wellfaserplatten. Beim Neubau sind sie also sehr viel günstiger als Dachziegel oder andere Dachdeckungen, die solare Strom-
erzeugung noch gar nicht eingerechnet. Somit zählt die Photovoltaik inzwischen zu den preiswertesten Baustoffen.
Damit relativieren sich die oben genannten Mehrkosten von Indach- und Fassadensystemen gegenüber Aufdachanlagen mit Standardmodulen. Insbesondere Indachanlagen sind sehr wirtschaftlich. In der Schweiz beispielsweise werden auf Einfamilienhäusern derzeit mehr Anlagen dachintegriert als über die Dachdeckung befestigt ausgeführt (Abb. 1).
Hoher Konstruktionsaufwand und schlechter Ausbildungsstand: Die angebotenen Indachsysteme sind zum Teil nicht praktikabel beziehungsweise installationsfreundlich. Oder sie besitzen andere Schwächen, insbesondere wenn die Dachform beziehungsweise die -deckung unüblich sind oder ein Dach durch viele Auf- oder Einbauten unterbrochen wird. Zudem sind die fachlichen Anforderungen bei der Planung und Installation hoch. Die korrekte Ausführung der Unterkonstruktion und die Einbindung in das Dach oder in die Fassade erfordert einiges an Fachwissen. Die beteiligten Akteure – Architekten, Bauplaner, Solarfachplaner und Installateure – besitzen bezüglich der PV-Integrationen häufig nur einen mangelhaften Wissensstand. Solarfirmen scheuen den Aufwand und konzentrieren sich auf die einfacheren Aufdachanlagen.
Aufwendige Projektkoordination und fehlende BIM-Modelle: BIPV-Projekte erfordern nicht nur eine aufwendige Projektkoordination, es mangelt zudem an standardisierten Planungsabläufen und definierten Bauablaufschnittstellen. Außerdem fehlen noch digitale PV-Modul-Modelle für das Building Integrated Modeling.
... und wer es ihr leichter machen will
Um die Hemmnisse abzubauen, hat sich ein Team aus Architekten, Bauplanern, Forschern und PV-Experten zusammengefunden. In dem vom Bundeswirtschaftsministerium geförderten Projekt Solar Envelope Center [3] stellen sie verfügbare technische Lösungen zusammen und erarbeiten Visualisierungsmöglichkeiten und Prozessoptimierungen sowie architektonisch, ökonomisch und technisch vorteilhafte Grundlösungen. Zudem entwickeln sie digitale Modelle für die computergestützte Planung und Visualisierung.
Unter der Leitung des Fraunhofer Instituts für Solare Energiesysteme ISE arbeiten in dem Projekt das Deutsche Forschungszentrum für Künstliche Intelligenz und der Landesverband Berlin Brandenburg der Deutschen Gesellschaft für Sonnenenergie (DGS) mit den Firmen Drees & Sommer Advanced Building Technologies und Wulf Architekten zusammen. Die DGS kümmert sich um die Verbesserung der regulatorischen und normativen Rahmenbedingungen. Und sie unterstützt die praktische Anwendung, insbesondere indem sie BIPV-Weiterbildungen für Architekten, Planer, Installateuren und andere Akteure erarbeitet (siehe www.dgs-berlin.de/termine).
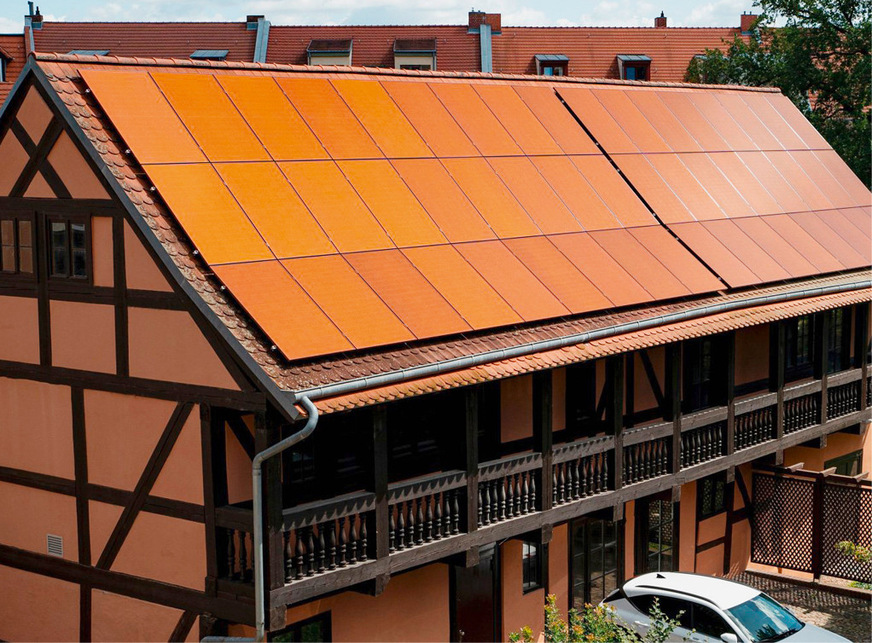
Bild: Futura Sun
Photovoltaik wird bunt
Die deutsche Solarbranche erhofft sich einen deutlichen Marktzuwachs in Richtung Gebäudeintegration. Ein Grund, der dafür spricht: Farbige Module sind in der Massenproduktion angekommen. Sie sprechen neue Anwendergruppen im Immobilienbereich an und eröffnen neue Anwendungsfälle. Sogar Gebäude, die unter Denkmal- oder Ensembleschutz stehen, lassen sich damit ausstatten (Abb. 2, siehe auch GEB 2024-10, Photovoltaik auf Baudenkmälern).
Das klassische Verfahren, um farbige Module herzustellen, ist die Verwendung von gefärbtem Glas. Bei gerahmten Modulen entspricht die Farbe des Rahmens der des Glases. Mehrere Hersteller bieten verschieden farbige PV-Module an. Eine andere Technik stellen farbige Folien dar, die in Module einlaminiert werden oder von außen aufgeklebt werden. Bei diesem Verfahren muss auf die Langzeitbeständigkeit der Folien und der Klebung geachtet werden. All diese Verfahren reduzieren allerdings den Wirkungsgrad signifikant (Abb. 3). Dabei gilt: Hellere Farben verursachen höhere Leistungsverluste als dunklere.
Die Forschung auf diesem Gebiet macht jedoch Fortschritte und ermöglicht durch Interferenzschichten, die Leistungsverluste deutlich zu senken. So entwickelte 2023 das Fraunhofer ISE die Morpho-Color-Technologie. Mit dieser Beschichtung wird eine gezielte Lichtbrechung erreicht, welche nur einen bestimmten Bestandteil des Lichtes reflektiert. Dadurch entsteht der gewünschte Farbeindruck. Gleichzeitig erreicht der größte Teil des Sonnenlichtes ungehindert die Oberfläche der Solarzelle. Inzwischen verwendet die Schweizer Firma Megasol das Verfahren bei der Herstellung ihrer farbigen Module.
Bei der neusten Entwicklung, die das Fraunhofer ISE im vergangenen Jahr vorgestellt hat, handelt es sich um eine Polymerfolie mit Mikrostruktur, die mit der Interferenzschicht versehen wird. Die Folie wird zwischen zwei Verkapselungsfolien eingelegt und in das PV-Modul einlaminiert. Weitere Interferenzverfahren werden mit speziellen Farbpigmenten der Firma Merck realisiert. Mit den Pigmenten lassen sich auch übliche Druckverfahren realisieren, was die Produktion vereinfacht. Dass farbige PV-Module inzwischen ein Thema in der Bau- und Solarbranche sind, zeigten die beiden Messen Intersolar im vergangenen Jahr und BAU in Januar 2025 in München.
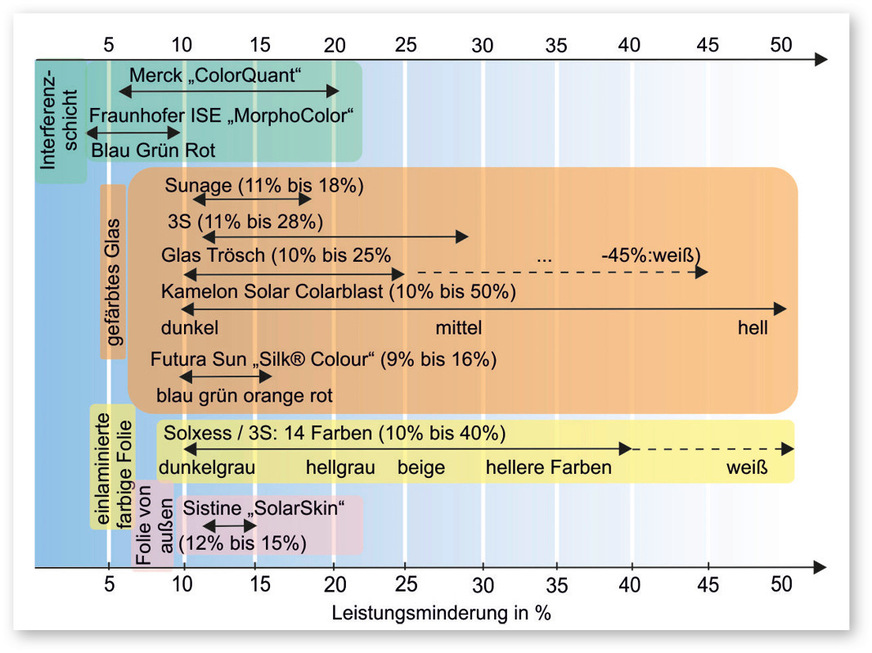
Bild: DGS
PV ins Dach integrieren
Ob farbig oder nicht – bei der Indachmontage befinden sich die PV-Module in der Ebene der herkömmlichen Dacheindeckung und ersetzen diese zum Teil, sodass Dachziegel und PV-Module eine verbundene Fläche bilden. Dadurch ergibt sich ein homogeneres und ästhetischeres Bild als bei klassischen Aufdachanlagen.
Prinzipiell lassen sich zwei Arten der Dachintegration unterscheiden. Zum einen können die PV-Module „geschindelt“ verlegt werden; sie sind dann so miteinander verbunden, dass sie ein regensicheres Solardach bilden. Oder zwischen den PV-Modulen kann Wasser eindringen. In diesem Fall muss unter ihnen eine Abdichtungsebene als wasserführende Schicht installiert werden (Abb. 4).
Als Dichtlage eignen sich überlagernde Kunststoffplatten, aber auch Bleche oder Dachdichtungsfolien sind möglich Durch die Bleche oder Platten werden Befestigungselemente oder Schienen an den Dachsparren verschraubt – am besten Schrauben mit EPDM-Dichtung dazu verwenden –, an denen sich die PV-Module beispielsweise mit Modulklemmen befestigen lassen. Den Abschluss an First, Ortgang und Traufe genauso wie den Anschluss an die herkömmliche Dachdeckung bilden spezielle Abschlussprofile und Anschlussbleche oder plissiertes Bleiband.
Bei einer echten Dachintegration stellen die Photovoltaikmodule die Regensicherheit her. Dafür überlagern sich die Module in der Horizontalen schindelartig. Das lässt sich entweder mit ungerahmten Modulen, mit speziell angepassten Modulrahmen oder mit einer zusätzlichen Rahmenkonstruktion, die gerahmte Standardmodule aufnimmt, umsetzen. Als typische Indachsysteme lassen sich nennen: Megaslate von 3S, Clearline fusion von Viridian Solar, nD-Indachsystem von nD-System, PV Indax von Braas, Solrif von Ernst Schweizer oder Tri-Roof+ von Tritec Energy.
Andere Hersteller bieten sogenannte Solardachziegel an, zum Beispiel Autarq, BMI Group, Jacobi-Walter, Nelskamp, Prefa Solar, Solteq und Sun Style. Die Produkte stellen häufig die ästhetisch ansprechendste Lösung dar, insbesondere bei anspruchsvollen Dachgeometrien, sind aber preislich im oberen Segment angesiedelt und erfordern mehr Aufwand und Geschick bei der handwerklichen Umsetzung.
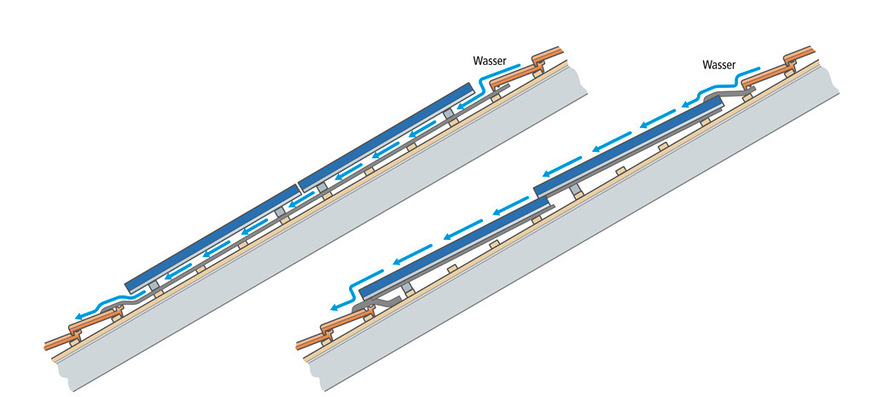
Bild: DGS
Module an die Fassade bringen
Auch bei Fassadensystemen gibt es einige Systeme, bei denen Schindlungen der PV-Module vorgenommen werden. Zudem werden oft Systeme für die vorgehängte hinterlüftete Fassade (VHF) angeboten, da sich Integration mit diesem System recht einfach realisieren lässt. Zudem ist VHF allgemein bekannt in der Bauwelt und in der MVV TB sowie den anderen Bauregeln gut beschrieben. Inzwischen sind von der Solarbranche diese Regeln um die Anforderungen der Photovoltaik ergänzt worden [4] [5].
Weitere Möglichkeiten bieten punkt- und linienförmige Befestigungen, zum Beispiel Glashalteleisten, oder geklebte Lösungen. Wie erwähnt sind je nach Anwendungsbereich, Gebäudeklasse, Höhe und Konstruktionsart baurechtlich zugelassene Module erforderlich. Standardmodule benötigen zumeist eine DIBt-Zustimmung im Einzelfall.
Mehrschalige Außenwandkonstruktionen, zum Beispiel VHF, werden auch als Kaltfassaden bezeichnet (Abb. 5). Den Witterungsschutz gewährleistet die vorgehängte Bekleidung. Dahinter folgt eine Luftschicht, danach die innere Schale aus Wärmedämmung, Dichtung und Konstruktion. Da die Fassadenbekleidung mit einem gewissen Abstand vor der Außenwand montiert ist, eignet sie sich hervorragend, um PV-Module aufzunehmen, denn die durch die Sonneneinstrahlung auftretenden Temperaturspitzen können über die Hinterlüftung ausreichend abgeführt werden. Zudem gibt es keine besonderen optischen Ansprüche bezüglich der Position und dem Aufbau der Anschlussdose auf der nicht sichtbaren Rückseite. Die Verkabelung kann in Kabelkanälen geführt werden, die im Bereich der Wärmedämmung an der tragenden Wand liegen.
Als Warmfassade werden einschalige Fassaden bezeichnet, deren Schichtenaufbau aus einem oder aus mehreren Materialien besteht (Abb. 6). Sowohl der äußere Witterungsschutz als auch der Wärmeschutz sind von der einschaligen Fassadenkonstruktion zu erfüllen (Sandwichpaneele, Wärmedämm-Verbundsysteme). Warmfassaden sind somit nicht hinterlüftet.
Die eingesetzten Fassadenelemente müssen einen niedrigen Wärmedurchgangskoeffizienten aufweisen. Ansonsten kann der Taupunkt in der Fassade liegen und sich Kondensat bilden. Dies kann entweder mit opaken Isolierpanelen oder transparenten oder semitransparenten Isoliergläsern erreicht werden. Warmfassaden werden in der Regel in Pfosten-Riegel-Konstruktion, in Elementbauweise oder in Brüstungsbauweise ausgeführt. Die wichtigsten technischen Merkmale von Vorhangfassaden sind in der Produktnorm DIN EN 13830 festgelegt.
In Warmfassaden können Isolierglas-PV-Module konventionelle Isolierverglasungen ersetzen. Bei ihnen münden die elektrischen Anschlüsse oft nicht in einer herkömmlichen rückseitigen Anschlussdose, um die Optik der Fassade nicht zu stören, sondern sie werden seitlich herausgeführt. Isolierglas-PV-Module sind aufwendig herzustellen und damit recht teuer. Einige spezialisierte Hersteller wie A2-Solar, Aleo Solar, Easy Fenster Göpper, Ertex Solar, Premium Solarglas, Sanko Solar, Schüco, und Sunovation bieten sie an. Bei opaken Warmfassaden können Standardmodule eingesetzt werden.

Bild: : www.pv-wissen.de
Weitere Fassadenkonstruktionen
Bei Pfosten-Riegel-Konstruktion (Abb. 7) werden Tragprofile mit Schraub- oder Steckverbindungen zu einer Rahmenkonstruktion zusammengefügt. Die senkrechten Stützen (Pfosten) sind durchgehend und werden an den Geschossdecken, seltener auch an tragfähigen Brüstungen oder an den Stützen des Skeletts befestigt, während die waagrechten Streben (Riegel) zwischen den Pfosten eingepasst werden. Alle Schnittstellen und Bohrungen können werkseitig nach der Bearbeitung durch eine Pulverbeschichtung gegen Korrosion geschützt werden.
Häufig werden die Füllelemente mit aufgeschraubten Pressleisten auf den Pfosten-Riegel-Profilen montiert. Dabei nimmt der Falzraum die Glasscheiben, Fassadenpaneele oder auch PV-Module gewissermaßen schwimmend auf und ist mit einem Dampfdruckausgleichs- und Entwässerungssystem versehen, das auftretendes Kondensat nach außen abführt. Außen verhindern durchlaufende Silikon- oder EPDM-Dichtungen das Eindringen von Wasser. Die Pfosten-Riegel-Konstruktion kann sowohl als Kalt- als auch Warmfassade ausgeführt werden.
Beim Structural Sealant Glazing (SSG) wird das Glaselement unmittelbar mit einem Adapterrahmen verklebt. Der Stahl- oder Aluminiumrahmen wird an der Unterkonstruktion – meist ein Pfosten-Riegel-System – befestigt. Dadurch lassen sich Fassadenflächen bauen, die von außen rahmen- und halterlos erscheinen. Die Verklebung muss grundsätzlich eine dafür zugelassene Werkstatt durchführen.
Adapterrahmen und Glas werden als Element gefertigt und auf der Baustelle in die Tragstruktur eingesetzt. Die Verklebung nimmt das Eigengewicht und die Windsogkräfte auf und wirkt gleichzeitig als Abdichtung. In Deutschland muss ab acht Meter Gebäudehöhe das Glasgewicht zusätzlich mechanisch gesichert werden, zum Beispiel über Haltewinkel. SSG ist ebenfalls sowohl für Kalt- als auch für Warmfassaden geeignet. Bei dieser Befestigungsart wird in der Regel eine Zustimmung des DIBt im Einzelfall erforderlich.